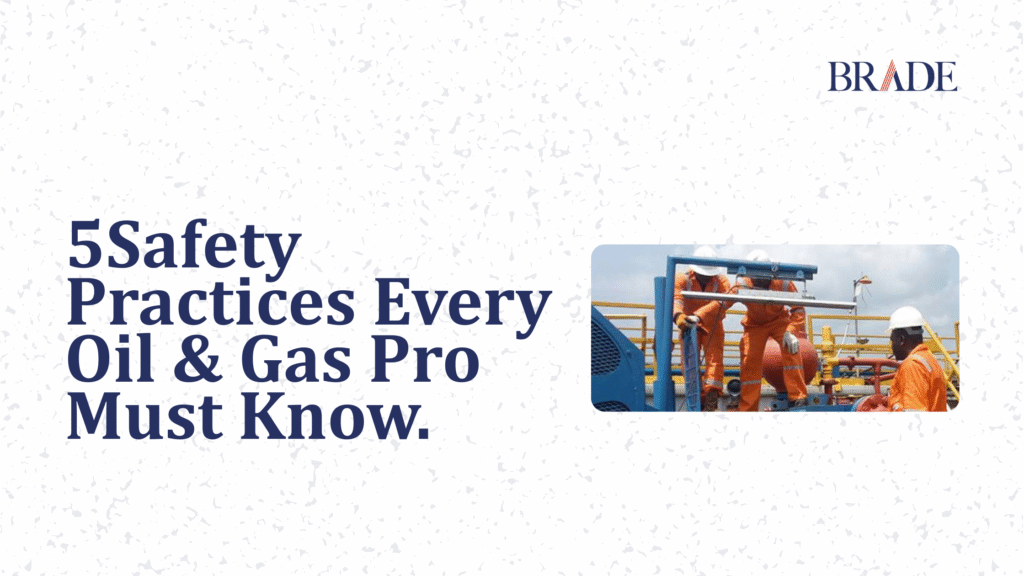
In the oil & gas industry, safety isn’t just a guideline; it’s a lifeline. With operations in remote locations, high-pressure environments, and hazardous conditions, the risks are significant. A single oversight can lead to catastrophic explosions, environmental disasters, regulatory shutdowns, or even loss of life.
For companies to remain operational, profitable, and compliant, they must establish a robust safety culture that prioritizes risk mitigation, proactive maintenance, and employee well-being. Here are essential safety best practices that every oil & gas professional must know, implement, and continuously improve.
1. Build an Unshakable Safety Culture
Safety starts with leadership, but it thrives when it becomes second nature to every worker. Companies with a strong safety culture reduce workplace incidents by up to 50% compared to those that only enforce compliance-based safety.
A strong safety culture isn’t just about policies, it’s about attitude, awareness, and accountability. When safety is ingrained in company values, employees at every level, from rig operators to executives, take ownership of workplace hazards and risk management.
To build a strong safety culture, there’s a need to establish strict safety policies with zero tolerance for negligence, conduct daily toolbox talks and shift handover safety briefings, and reward proactive safety behavior to reinforce a positive safety culture.
2. Conduct Rigorous Risk Assessments & Hazard Analysis
Every oil and gas operation carries inherent risks, from fire hazards to high-pressure systems and toxic gases. A comprehensive Risk Assessment & Hazard Analysis (RAHA) can prevent potential disasters.
To improve risk management, conduct Job Safety Analysis (JSA) before initiating any high-risk task to identify potential hazards. Utilize HAZOP (Hazard and Operability) studies to systematically assess and mitigate possible process failures. Additionally, deploy real-time monitoring systems to detect abnormal pressure fluctuations, gas leaks, or equipment malfunctions before they escalate into critical incidents.
Also, update risk assessments regularly to account for changing worksite conditions.
3. Enforce Proper Personal Protective Equipment (PPE) Compliance
As the last line of defense in hazardous environments, Personal Protective Equipment (PPE) plays a vital role in safeguarding workers. However, improper use or inadequate gear remains a persistent issue, with industry data revealing that PPE non-compliance contributes to nearly one-third of all workplace injuries in oil & gas.
To strengthen PPE compliance, companies must ensure that workers have task-specific protective gear, including fire-resistant clothing (FRC), impact gloves, safety harnesses, and gas masks, tailored to the risks they face. Routine PPE inspections are essential to identify worn-out or damaged equipment before it compromises safety.
Training programs should reinforce proper donning, doffing, and storage procedures, ensuring that employees know how to wear and maintain their protective gear correctly. Additionally, smart PPE technology, equipped with gas detection sensors and worker fatigue monitoring, is revolutionizing workplace safety by providing real-time data that enhances hazard prevention and response.
4. Implement a Robust Permit-to-Work (PTW) System
A Permit-to-Work (PTW) system ensures that high-risk activities, like hot work, confined space entry, and electrical maintenance, are properly controlled and authorized. Effective PTW requires written approval before hazardous tasks, digital tracking for real-time oversight, and integration with gas detection and fire suppression systems for added safety. Competent personnel must oversee compliance to prevent lapses.
The 2005 Texas City Refinery Explosion, which killed 15 workers, underscores the dangers of weak permit controls, emphasizing the need for strict enforcement.
5. Strengthen Process Safety Management (PSM)
Process Safety Management (PSM) focuses on preventing catastrophic failures by ensuring equipment, procedures, and personnel operate in sync. Strengthening PSM requires regular equipment integrity checks to prevent corrosion and failures, automated emergency shutoff valves to manage unexpected process upsets, and comprehensive training in Process Hazard Analysis (PHA) and emergency response protocols.
Clear Management of Change (MOC) procedures must be in place to safely implement operational modifications. Refineries that follow stringent PSM guidelines experience 60% fewer unplanned shutdowns and major accidents, reinforcing the critical role of proactive safety management.
Safety in oil & gas is about creating a culture where risk awareness, proactive measures, and accountability become second nature. Establishing a strong safety culture, conducting rigorous risk assessments, enforcing PPE compliance, implementing robust permit-to-work systems, and strengthening process safety management lays the foundation for an incident-free work environment.
But safety doesn’t stop here. Preventing fires, handling hazardous materials, ensuring vehicle safety, prioritizing worker well-being, and committing to continuous training are just as critical, Because in this industry, safety isn’t optional, it’s the foundation of success.
So, are you ready to take safety to the next level?
Start by assessing your current practices. Where does your team stand?
Share this guide with your crew, spark a conversation, and commit to raising the bar on safety.